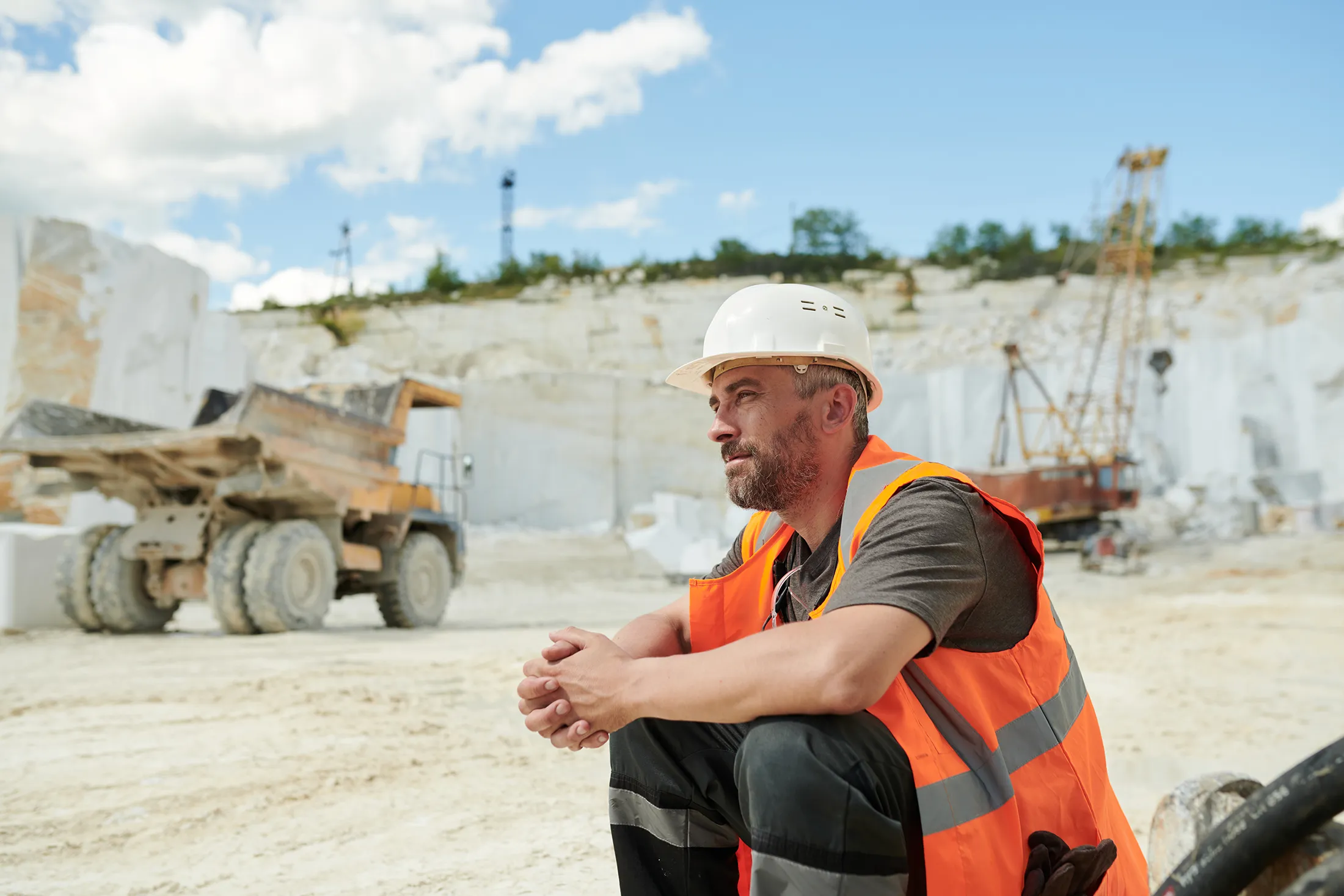
From Ports to Warehouses: Groundwork Behind the Logistics Boom
As the logistics sector expands rapidly, massive warehouses and port facilities require specialized foundation solutions. Discover how dynamic compaction techniques from Densification Inc. create the stable foundations that keep global supply chains moving.
The Hidden Challenge of Logistics Infrastructure
The modern logistics boom is clear in the many delivery vehicles on our roads. It is based on large warehouses, distribution centers, and port facilities. These places are the backbone of global trade. These critical hubs face a challenge invisible to most: the soil beneath them.
Many logistics facilities are constructed on challenging sites:
- Former industrial lands with variable fill material
- Coastal areas with loose alluvial soils
- Reclaimed land with inconsistent compaction
- Brownfield sites with unpredictable subsurface conditions
Without proper ground improvement, these facilities risk:
- Uneven settlement causing cracked floor slabs
- Foundation issues affecting rack stability
- Reduced load-bearing capacity limiting operations
- Costly repairs and operational disruptions
As the demand for logistics space grows, warehouse construction is hitting record levels in 2024. This makes the need for specialized ground improvement solutions more important than ever.
Understand Ground Densification Technology
Site-Specific Geotechnical Analysis
What sets Densification Inc. apart is our commitment to precision. Before any tamper hits the ground, our geotechnical engineers conduct comprehensive site assessments including:
- Soil borings and sampling to identify subsurface conditions
- Laboratory testing to determine soil properties
- Cone penetration tests (CPT) to measure in situ density
- Historical site analysis to identify fill areas
This data helps us calibrate our energy process. It determines the exact weight, drop height, and grid pattern needed to reach target densification levels across the site.
Real-World Applications in Logistics Development
Port Expansion Projects
Modern ports handle unprecedented cargo volumes, with container ships now carrying over 24,000 TEUs (twenty-foot equivalent units). This requires:
- Heavily reinforced quay walls and aprons
- Stable foundations for massive ship-to-shore cranes
- Uniform settlement characteristics under heavy loads
At the Port of Oakland expansion, Densification Inc. used deep dynamic compaction. This method stabilized over 120 acres of reclaimed land. It created a strong foundation that can support container stacks six units high. The specialized pattern of drops ensured uniform bearing capacity across the entire terminal area.
Distribution Center Development
E-commerce growth has driven demand for massive fulfillment centers, often exceeding 1 million square feet. These facilities require:
- Crack-resistant floor slabs for material handling equipment
- Uniform support for high-bay racking systems
- Stable foundations for automated storage and retrieval systems
Our work at the Bridge Point Commerce Center demonstrates our expertise in this area. By implementing a systematic dynamic compaction program, we:
- Increased soil bearing capacity by 25%
- Reduced differential settlement potential by 60%
- Enabled the use of cost-effective shallow foundations
- Compressed the construction schedule by eliminating deep foundation requirements
AGP Construction reports that the 450,000-square-foot facility now holds millions of pounds of inventory. The slabs have stayed crack-free for years after construction.
The Business Case for Ground Improvement
Cost-Effectiveness in Logistics Development
For developers and project managers in the logistics sector, dynamic compaction offers compelling economic advantages:
- Lower foundation costs: By improving the soil on site, developers can often avoid deep pile foundations. This can save 15-30% on foundation costs.
- Accelerated construction timelines: Dynamic compaction can quickly treat large areas. It can cover up to 3 acres per week in the best conditions. This helps reduce overall project schedules.
- Sustainable construction: By improving existing soils rather than removing and replacing them, this approach reduces truck traffic, material disposal, and imported fill requirements.
- Lower long-term maintenance costs: Well-compacted soils reduce settlement problems. This helps avoid expensive floor repairs and operational issues.
Case Study: Bridge Point Commerce Center
The economic impact of proper ground improvement is clearly illustrated in our work at Bridge Point Commerce Center, where:
- Initial site assessment revealed loose fill extending to depths of 28 feet
- Standard foundation designs would have required over 2,000 individual piles
- Dynamic compaction permitted shallow foundation systems throughout
- The project schedule was reduced by 45 days
- Overall foundation costs decreased by approximately $2.8 million
This project exemplifies why Densification Inc. has become the preferred ground improvement contractor for major logistics developers nationwide
Advanced Techniques for Challenging Sites
For particularly challenging logistics sites, Densification Inc. employs specialized variations of dynamic compaction:
Rapid Impact Compaction (RIC)
For sites with sensitive neighboring structures or areas requiring precise energy control, rapid impact compaction offers:
- Controlled, high-frequency impacts
- Excellent for upper soil layers (0-15 feet)
- Minimal vibration impact on adjacent properties
- Real-time monitoring and quality control
Hybrid Compaction Approaches
Many logistics sites benefit from combined treatment approaches:
- Dynamic compaction for deep densification
- Rapid impact compaction for precision finishing
- Stone columns or aggregate piers in areas requiring additional support
- Surcharge preloading for sites with significant clay content
Densification Inc. ensures optimal results across diverse soil profiles by tailoring our approach to specific site conditions.
The Future of Logistics Ground Improvement
As the logistics sector continues to evolve, ground improvement technologies are advancing to meet new challenges:
- Automated monitoring systems provide real-time density measurements during compaction
- 3D subsurface modeling allows precise targeting of problem areas
- Sustainable additives enhance traditional densification in environmentally sensitive areas
- Carbon-reduced approaches minimize the environmental impact of ground improvement
Densification Inc. remains at the forefront of these innovations, continuously refining our approach to deliver stronger, more resilient foundations for tomorrow’s logistics infrastructure.
Conclusion: Building the Foundation for Supply Chain Resilience
The ongoing logistics boom demands an infrastructure that can withstand unprecedented operational demands. The large warehouses and port facilities that support global trade are easy to see. However, their long-term success relies on the unseen work happening below them.
As a leading ground densification contractor, Densification Inc. provides the specialized expertise needed to transform challenging sites into stable platforms for logistics operations. We use dynamic compaction and deep dynamic compaction to build strong foundations. These foundations support buildings and the whole supply chain.
For developers, engineers, and project managers navigating logistics construction, partnering with experienced ground improvement specialists is essential. Densification Inc. provides the expertise, specialized tools, and a strong history. This ensures your logistics facilities are built on solid ground now and for many years ahead.
Contact Densification Inc. today. Let’s talk about your logistics project’s ground improvement needs. Discover how our dynamic compaction services can make your site better for long-term performance.